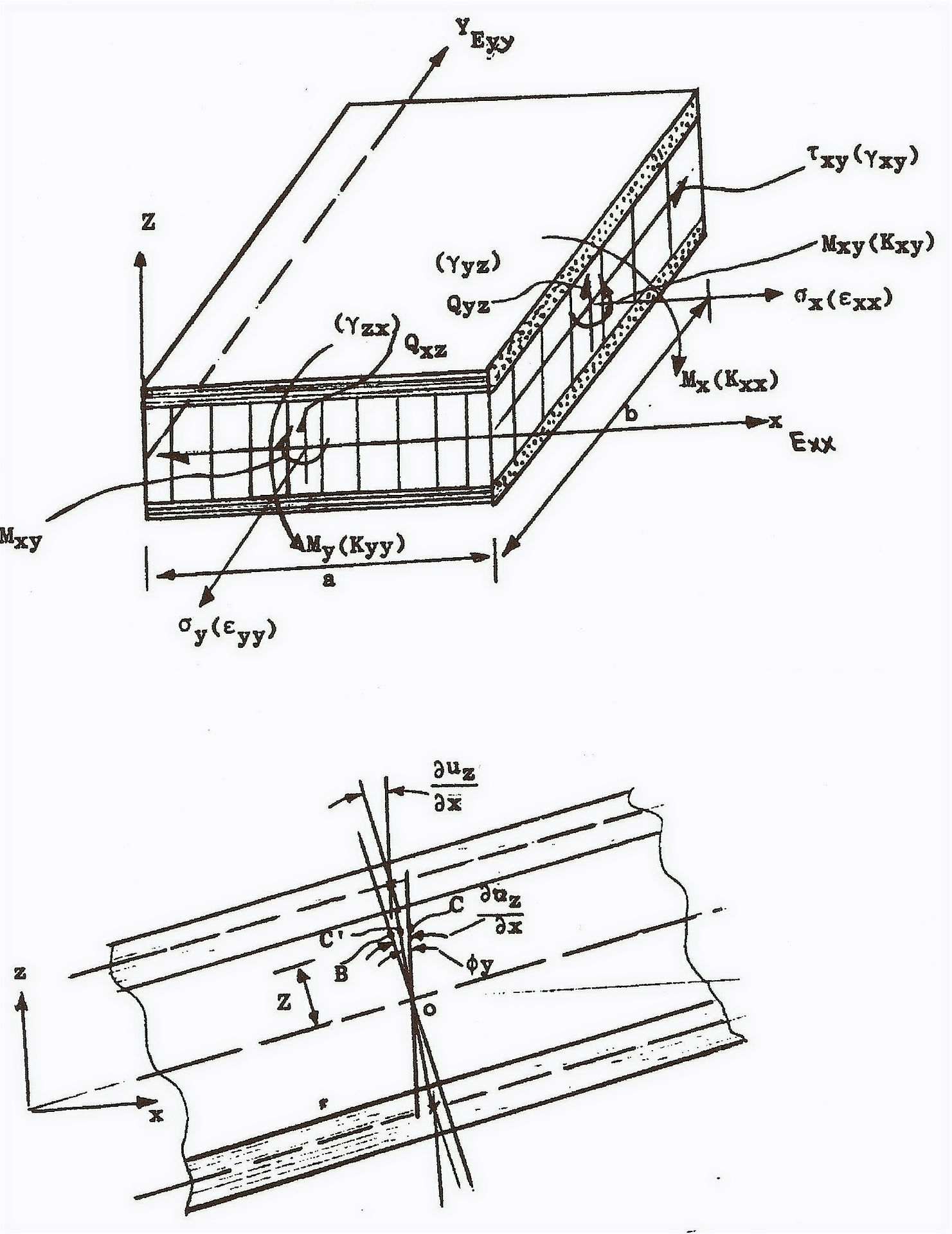

Lightweight & Composite Structures
Aero-structures
We provide cost-effectively optimised design & analysis solutions for primary & secondary composite and metallic structures. Our experience covers a wide range of aero-structural parts:
-
CFRP wing and fuselage structures
-
High-lift device (flaps) certification analysis and documentation
-
Helicopter CFRP Nomex sandwich structures of fuselage, empennage
-
Spacecraft– Sandwich structures payload module
-
Engine– Nacelle and reverse thrust structures
-
Business jet CFRP structures, empennage, VTP and HTP
-
All composite light aircraft trainer
-
Fuel tank (Metallic Stiffened panel) pressure tests & certification stress report.
-
Aircraft interior stress analysis and report (seats and galleys)
Design and Analysis Capability
From involvement and experience in previous projects in the design and analysis of aero-structures with metallic and composite constructions, we provide technical consultancy services for the following topics:
-
Concept and configuration Analysis
-
Static/Fatigue Analysis, Check Stress and Certification documentation
-
Stiffened Panel Structures
-
Honeycomb / Foam Sandwich Panel Structures
-
Fatigue & Damage Tolerance
-
Bolted and Bonded Joints Analysis
-
Thermal Analysis
-
Buckling Analysis
-
Vibration & Modal Analysis
-
Non-Linear Analysis
-
Testing – Procedures and Support
Our analysis and simulation services are supported by our ability to specify qualification and material testing for component validation.
We use the following design and analysis tools:
CAD: Catia V5 and Solid Works. FEM: MSC Nastran/Patran for static & linear problems, Abaqus for non-linear issues such as material studies, large deformation analysis, contact and impact simulations.
Structural Optimisation: Aero Optimal Optimisation software tool
Manual calculations remain an essential part of our analysis services.

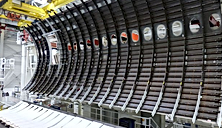
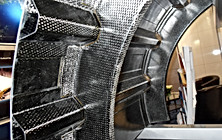


.png)

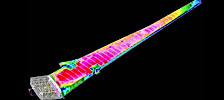
